The 5 Phases of Workloading a Facility
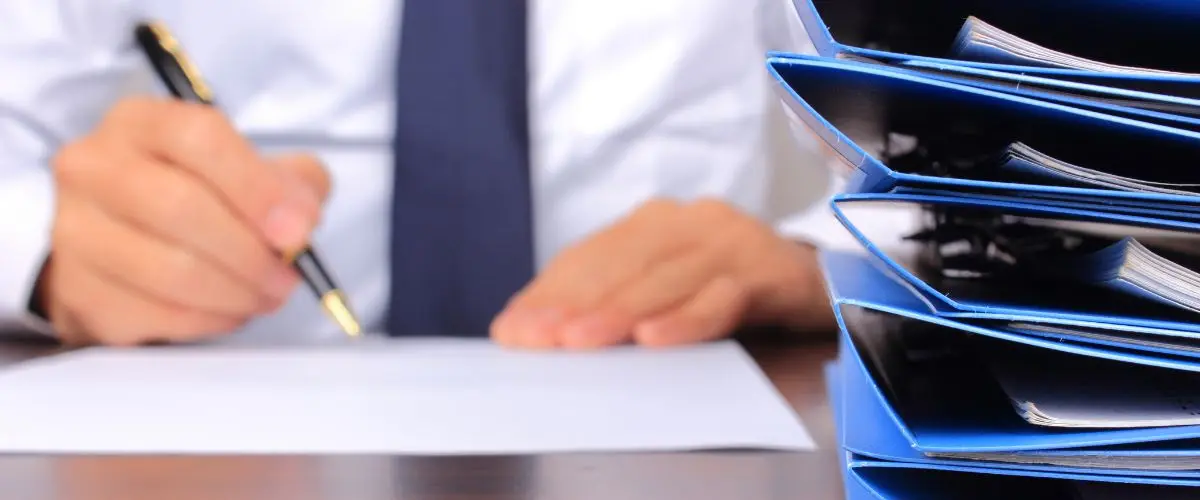
Maintaining a facility is like building a house – you need a blueprint. With a blueprint, your vision suddenly becomes a concrete, documented, executable work plan. That’s what workloading is – creating a plan that becomes a repeatable process for a clean and healthy facility. Every cleaning manager should thoughtfully workload their facility to give their staff the best chance for success. Below, I will outline the 5 phases of successfully workloading a facility.
1. Identify Production Rates
First things first, write down all the tasks currently performed in your facility. Start with the big bucket items: restrooms, entryways, above the floor cleaning, floor care, restrooms, trash, and utility work. Then, work towards specific and project tasks. Once you’ve written down all your cleaning tasks, look up the production rates for those tasks in the ISSA Cleaning Times and Tasks Handbook. Next, consider the available options. Can you improve production rates with new equipment or techniques? What investments are feasible for your facility this year and in the years to come?
2. Customize Production Rates
Once you’ve pulled rates from the ISSA standard, customize the production rates to your facility. Take into account cleanable square footage, size of restrooms, and number of restroom fixtures. Also look at areas where your crew has limited access to clean. Do you have to clean before or after people are in their offices? Also factor safety into consideration. For example, how are you cleaning occupied areas? Can you reduce or remove trip and slip hazards?
3. Design the Plan
Phase three is where you’ll actually get into workloading. First you need to assign the work to your staff. Try and divide tasks in a fair and representative way, so that all of your employees are carrying as close to the same load as possible. When dividing the work, take these questions into consideration:
- Does everyone work full-time?
- Do we hire part-timers?
- Who works which shift?
- When does routine and project work happen?
- What are the physical limitations of your workers?
Once you’ve answered these questions, design a system based on your workforce, schedule, and cleanable hours. At the end of the design phase, gather any new tools and materials necessary to implement your plan.
4. Communicate the Plan
Once you’ve created your plan, you need to communicate to both your staff and customers. Successfully communicating the how and why of your new program will set it up for success. Train your staff in any new protocols and be sure to communicate with your customer the benefits of the changes you are making. (For more on implementing change, my colleague Marc Ferguson does a great job outlining the steps to change management here.)
5. Revisit and Revise
Remember that this is a journey, not a destination. Your first plan may look better on paper than it does in practice. Take the lessons you learn from your initial implementation and apply them until you have a system in place that works for your facility’s needs.
Workloading is the engine that drives cleaning change. I hope that this outline of the five phases of workloading will help you create a more efficient cleaning program.